【導讀】防錯與組裝后檢查完全不同,后可能導致潛在的返工或零件報廢。防錯的本質是以不會發(fā)生錯誤或失敗的方式設計裝配過程。它既積極主動又具有預防性。以下是這些傳感器執(zhí)行的六個有價值的功能以及典型的應用示例。
在所有行業(yè)中,自動和手動裝配程序的防錯功能的顯著優(yōu)勢越來越明顯。目標是提高質量和提高生產(chǎn)力。通常提高生產(chǎn)力是以質量為代價的。但是,使用新的傳感器技術,可以在過程中自動驗證組件并防錯,而不是后處理。這節(jié)省了制造過程中的步驟,并消除了顯著的成本。可以應用高精度光電傳感器,尺寸測量傳感器,光幕和基于攝像頭的技術以及手動技術來確保關鍵的產(chǎn)品屬性。并且這些相同的技術也可用于測量和評估隨時間的過程變化。
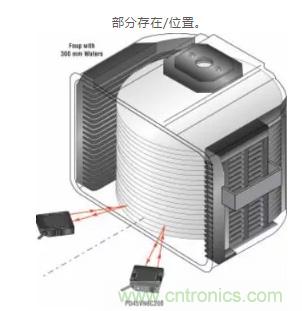
部分存在/位置
在流程的下一步驟之前驗證關鍵部件是否到位并處于正確位置是一項常見要求。光電傳感器可以輕松實現(xiàn)這一目標,最新型號甚至可以檢測零件的最小和最窄邊緣。在圖示中,兩個傳感器可以形成僅為百分之一英寸的會聚點,以精確地檢測半導體晶片的邊緣。在該示例中,傳感器不僅驗證晶片的存在,而且還可以檢測晶片是否在盒中傾斜。
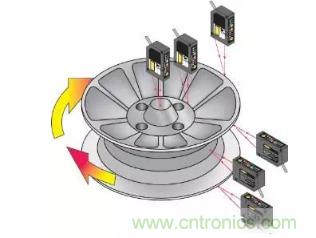
短程測量
隨著過去幾年傳感技術的進步,用戶現(xiàn)在能夠將具有成本效益的測量功能集成到他們的工藝中,分辨率高達0.0001英寸。在下一個制造步驟之前,可以自動檢查零件的關鍵屬性。在圖示中,激光傳感器檢查在夾具中旋轉的鑄造輪,以確保在加工之前沒有空隙或過多的跳動。
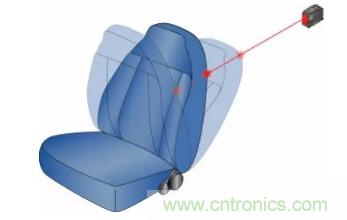
遠程測量
新的遠程傳感器可以在機器或過程中查看較短距離的傳感器不適合或存活,或者干擾該過程。現(xiàn)在可以在1到164英尺的任何距離進行巡檢,重復精度為0.04到0.12英寸。該功能開辟了數(shù)千種新的檢測應用。該圖顯示了單個傳感器測量汽車座椅靠背的運動范圍,以驗證它能夠在三個傾斜角度進行調整,而不考慮座椅材料,顏色或紋理。
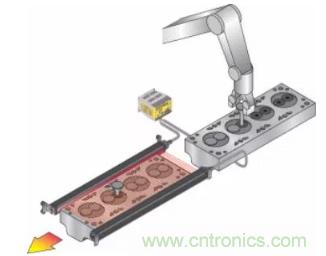
光幕部分剖析
傳統(tǒng)的單光束傳感器無法檢查許多零件或組件。通常,用戶需要確定幾個部件中的任何一個或多個部件是否處于組件上的適當位置。光幕系統(tǒng)可以對整個零件進行輪廓分析,以查找丟失或放錯位置的組件。在該示例中,光幕正在檢查氣缸蓋的表面以確保在自動裝配過程中所有閥門都安置在頭部中。
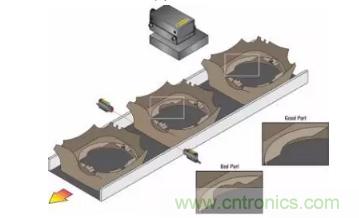
圖像識別
通常必須檢查整個產(chǎn)品區(qū)域,因為缺陷可能位于特定區(qū)域的任何位置。圖像傳感器旨在通過計算像素的相機輕松解決這些應用,然后將計數(shù)與預先確定的參考計數(shù)進行比較。在應用示例中,傳感器檢查塑料轉向柱部件是否存在法蘭區(qū)域中的不規(guī)則性,并且與良好部件相比,拒絕記錄80%或更少白色像素的部件。
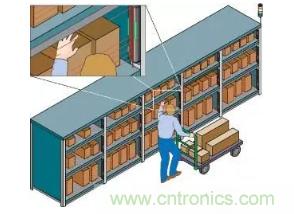
手動箱檢驗驗證
順序手動裝配中人的準確性也是防錯的一個大問題。PLC控制的“揀選”系統(tǒng)使用指示下一個要選擇的項目的燈,以及每個箱前面的光幕來驗證是否已經(jīng)采取了正確的部件。這些系統(tǒng)通過減少錯過的零件以及以錯誤順序組裝的零件來提高裝配操作的質量百分比。除了裝配過程的防錯之外,它們還通過在裝配過程中始終驗證裝配工最后停止的位置來提高工人效率,即使在休息或停工之后也是如此。這種完全可視化的通信系統(tǒng)也是一種全球解決方案,可消除語言障礙和技術能力等培訓障礙。該圖顯示了倉庫應用程序。
在今天的市場中,簡單地制作零件并不夠好。制造商和客戶要求對每個零件或組件都具有可測量和可驗證的高質量。除了降低廢品和廢料百分比之外,防錯還可以減少質量檢驗和返工所花費的時間。這加起來降低了制造成本并提高了工廠的盈利能力。制造商現(xiàn)在能夠以前所未有的速度優(yōu)化生產(chǎn)速度并生產(chǎn)優(yōu)質產(chǎn)品。